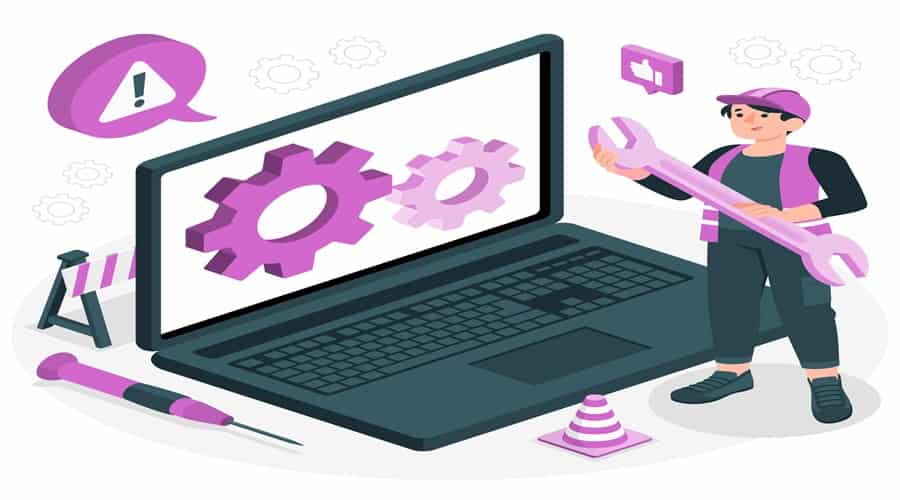
Streamline Your Maintenance Operations with CMMS Software
Effective maintenance operations guarantee business continuity, optimize asset longevity and reduce expensive downtime in today’s fast-paced industrial and facilities management environment. Computerized maintenance management system (CMMS) software has become a potent tool for streamlining and optimizing maintenance processes. It can manage assets, schedule preventive maintenance, track work orders, and analyze performance data.
Understanding the Importance of CMMS
A well-implemented Computerized Maintenance Management System (CMMS) solution offers numerous advantages over traditional manual maintenance processes. These benefits streamline maintenance operations, improve asset management, and enhance efficiency. Here are some key advantages of implementing a CMMS solution:
Improved Asset Management:
Centralized Tracking: CMMS provides a centralized platform for tracking and monitoring all assets, including equipment, facilities, and infrastructure. This centralized database ensures that maintenance teams have accurate and up-to-date information about each asset’s status, location, and maintenance history.
Detailed Asset Records: Maintain comprehensive records of each asset’s specifications, warranty information, and maintenance activities, facilitating better asset management and decision-making.
Preventive Maintenance Planning:
Scheduled Maintenance: Preventive maintenance tasks can be scheduled and automated with the help of CMMS software. By being proactive, you may increase the lifespan of your assets and lower the chance of unplanned malfunctions.
Task Automation: Automate routine maintenance tasks based on usage, time intervals, or condition-based triggers to ensure timely maintenance without manual intervention.
Work Order Management:
Streamlined Processes: A CMMS streamlines the creation, assignment, and tracking of work orders, making maintenance operations more efficient. This ensures that maintenance tasks are completed promptly and that technicians know their responsibilities.
Real-time Updates: Monitor the status of work orders in real-time, allowing for better oversight and the ability to address issues as they arise quickly.
Inventory and Spare Parts Control:
Optimized Inventory Levels: CMMS helps optimize inventory levels by monitoring and managing spare parts. This prevents overstocking and stockouts and ensures that necessary parts are available when needed.
Automated Reordering: Set up automated reordering based on predefined thresholds to ensure critical spare parts are restocked before running out.
Data-Driven Decision Making:
Maintenance Data Analysis: CMMS software collects and analyzes maintenance data, providing insights into asset performance, maintenance costs, and areas for improvement. This data-driven approach helps maintenance managers make informed decisions.
Performance Metrics: Monitor critical performance metrics (KPIs) like mean time between failures (MTBF) and mean time to repair (MTTR) to spot patterns and chances to improve maintenance procedures.
Key Features and Functionality of CMMS Software
Effective CMMS software typically includes robust features and functionalities designed to streamline maintenance operations and improve overall efficiency. Here are some of the key features and functionality you can expect from a comprehensive CMMS solution:
Asset Management:
Comprehensive Asset Tracking:
Maintain detailed records of all assets, including information about their location, condition, and maintenance history. This centralized tracking helps ensure that maintenance teams have accurate and up-to-date information about each asset.
Asset Lifecycle Management:
Monitoring an asset’s whole lifecycle, from purchase to disposal, can help with asset investment planning and management.
Work Order Management:
Creation and Assignment:
Simplify the creation and assignment of work orders for maintenance tasks. Assign work orders to specific technicians or teams based on availability, skills, and workload.
Prioritization and Tracking:
Sort work orders according to their significance and urgency. Monitor the current status of every work order in real time to guarantee prompt completion and responsibility.
Work Order Templates:
Use predefined templates for common maintenance tasks to streamline the work order creation process and ensure consistency.
Preventive Maintenance Scheduling:
Automated Scheduling:
Schedule preventative maintenance automatically using consumption, time intervals, or condition-based triggers. This proactive strategy prolongs the life of assets and helps avoid unplanned breakdowns.
Task Notifications:
Set up notifications and reminders to alert maintenance teams of upcoming preventive maintenance tasks and ensure they are completed on time.
Inventory and Spare Parts Management:
Inventory Tracking:
Track inventory levels of spare parts and consumables. Monitor stock levels in real time to prevent overstocking or stockouts.
Optimized Inventory Levels:
Analyze usage patterns to optimize inventory levels and reduce carrying costs. Set up automated reordering based on predefined thresholds to ensure critical parts are always available.
Supplier Management:
Maintain records of suppliers and track their performance to ensure timely delivery and quality of spare parts.
Reporting and Analytics:
Customizable Reports:
Provide customizable reports and dashboards for performance analysis. Analyze significant data such as mean time to repair (MTTR), mean time between failures (MTBF), and maintenance expenses.
Data-Driven Decision Making:
Use data insights to pinpoint problem areas, enhance maintenance plans, and arrive at wise choices.
Mobile Access:
Field Access:
Allow technicians to access and update information from the field using mobile devices. This will ensure that they have the latest information at their fingertips and can record maintenance activities in real-time.
Offline Capabilities:
Allow technicians to continue working even in areas without internet connectivity. Sync data once they are back online to ensure no information is lost.
Benefits of Implementing CMMS Solutions
Implementing a CMMS (Computerized Maintenance Management System) solution can benefit organizations by transforming maintenance operations and enhancing overall efficiency. Here are some of the key benefits:
Increased Equipment Uptime and Reliability:
Proactive Maintenance:
CMMS solutions enable the scheduling and automation of preventive maintenance tasks, reducing the likelihood of unexpected breakdowns and ensuring that equipment operates reliably.
Timely Repairs:
By streamlining work order management, CMMS ensures that maintenance tasks are completed promptly, minimizing downtime and keeping equipment running smoothly.
Reduced Maintenance Costs and Inventory Carrying Costs:
Cost-Effective Maintenance:
By streamlining maintenance schedules and prioritizing preventative maintenance, a company may prolong the life of its assets and save money on expensive emergency repairs.
Optimized Inventory Levels:
CMMS helps monitor and manage spare parts inventory, reducing excess stock and minimizing the carrying costs of maintaining large inventories. Automated reordering ensures that critical parts are available when needed, preventing stockouts.
Improved Productivity and Efficiency of Maintenance Teams:
Streamlined Workflows:
CMMS automates and simplifies maintenance processes, from work order creation to completion. This reduces administrative tasks and allows maintenance teams to focus on their core responsibilities.
Resource Allocation:
The software provides insights into the availability and workload of technicians, helping managers allocate resources more effectively and ensuring that the right personnel are assigned to the right tasks.
Enhanced Compliance and Regulatory Adherence:
Accurate Record-Keeping:
By keeping thorough records of every maintenance task, CMMS guarantees that companies can quickly retrieve past information and prove they adhere to industry norms and requirements.
Scheduled Inspections:
The software can plan and monitor regulatory inspections and audits to guarantee that compliance requirements are fulfilled and lower the possibility of fines and penalties.
Extended Asset Lifespan and Optimized Maintenance Cycles:
Lifecycle Management:
CMMS tracks the entire lifecycle of assets, from acquisition to disposal, enabling organizations to plan and execute maintenance activities that maximize asset lifespan and performance.
Predictive Maintenance:
Advanced CMMS solutions that can interface with IoT sensors and other technologies make predictive maintenance possible. This allows for identifying problems before they become serious and optimizing maintenance cycles using real-time data.
Data-Driven Decision-Making and Continuous Improvement:
Performance Analytics:
CMMS offers strong reporting and analytics capabilities that provide maintenance performance, expenses, and asset health information. These insights can help managers identify areas for development and make wise decisions.
Continuous Improvement:
Organizations can implement continuous improvement initiatives by analyzing maintenance data and trends, refining their maintenance strategies, and achieving better results over time.
Criteria for Selecting the Right CMMS Software
It’s critical to consider a number of factors when analyzing CMMS (Computerized Maintenance Management System) software options to ensure the solution you select will fulfill your company’s unique requirements. The following are the essential considerations:
Industry-Specific Features and Compliance Requirements:
Tailored Functionality:
Ensure the CMMS software offers features tailored to your industry, whether manufacturing, healthcare, facilities management, or another sector. Industry-specific functionality can address unique maintenance challenges and compliance requirements.
Regulatory Compliance:
Check if the software supports compliance with relevant regulations and standards, such as OSHA, ISO, or FDA guidelines, which can be critical for certain industries.
Scalability and Flexibility to Accommodate Future Growth:
Growth Potential:
Select a CMMS that will expand with your company as it expands. This entails managing a growing number of resources, users, and places without sacrificing efficiency.
Flexible Configuration:
Look for software that offers flexibility in configuration and customization, allowing you to adapt to changing business needs and processes.
Integration Capabilities with Existing Systems and Technologies:
Seamless Integration:
Ensure the CMMS can integrate smoothly with your existing systems, such as ERP, accounting, HR, and other enterprise applications. Integration facilitates data sharing and streamlines workflows.
IoT and Predictive Maintenance:
Consider whether the CMMS supports integrating IoT devices and sensors for real-time monitoring and predictive maintenance capabilities.
User-Friendliness and Ease of Adoption:
Intuitive Interface:
Choose software with an intuitive interface that is simple for your maintenance staff to understand and operate. A complex system might result in inefficiencies and low adoption rates.
Training and Onboarding:
Evaluate the training and onboarding resources provided by the vendor. Comprehensive training materials, tutorials, and support can facilitate a smooth transition to the new system.
Vendor Reputation, Support, and Training Offerings:
Vendor Credibility:
Examine the vendor’s standing in the industry. Look for case studies, testimonials, and customer reviews to learn about other companies’ experiences.
Customer Support:
Evaluate the vendor’s level of customer service. Responsive and dependable support can be essential for resolving problems and successfully implementing and running the CMMS.
Training Services:
Consider the availability of training services and resources, including in-person training, online courses, webinars, and documentation.
Total Cost of Ownership (TCO) and Pricing Models:
Upfront and Ongoing Costs:
Analyze the total cost of ownership, including upfront costs, subscription fees, implementation costs, training expenses, and ongoing maintenance and support fees.
Pricing Models:
Examine several price structures, including pay-as-you-go, perpetual licenses, and subscription-based pricing. Select a model that fits into your spending plan and financial schedule.
Industry-Leading CMMS Software Options
Fiix
Description:
Fiix is a user-friendly CMMS software designed to help businesses manage their maintenance operations efficiently. It offers robust asset management, work order management, and preventive maintenance scheduling features.
Pros:
Intuitive interface, strong mobile support, excellent customer service.
Cons:
It can be expensive for smaller organizations.
Mainly Used For:
Manufacturing, facilities management, and utilities.
Pricing Package:
Subscription-based pricing with various tiers.
UpKeep
Description:
UpKeep is a mobile-first CMMS that allows maintenance teams to manage work orders, track assets, and schedule preventive maintenance from their smartphones.
Pros:
Mobile accessibility, ease of use, real-time updates.
Cons:
Less advanced features in lower-tier plans.
Mainly Used For:
Manufacturing, property management, healthcare.
Pricing Package:
Monthly subscription plans, including a free tier for small teams.
IBM Maximo
Description:
IBM Maximo, an enterprise asset management (EAM) system, offers great functionality for managing assets, work orders, inventories, and procurement.
Pros:
Highly customizable, robust feature set, suitable for large enterprises.
Cons:
High cost, steep learning curve.
Mainly Used For:
Large-scale industries like oil & gas, utilities, transportation.
Pricing Package:
Subscription-based pricing with enterprise licensing options.
Hippo CMMS
Description:
Hippo CMMS is a user-friendly maintenance management software that offers asset management, work order management, and preventive maintenance features.
Pros:
Easy to use, affordable pricing, good customer support.
Cons:
More advanced features compared to competitors.
Mainly Used For:
Healthcare, education, manufacturing.
Pricing Package:
Subscription-based pricing with different tiers.
Maintenance Connection
Description:
Maintenance Connection is a comprehensive CMMS solution that provides tools for asset management, work order tracking, and preventive maintenance.
Pros:
Extensive reporting capabilities, scalable for different business sizes.
Cons:
The initial setup can be complex.
Mainly Used For:
Manufacturing, healthcare, facilities management.
Pricing Package:
Subscription-based pricing customized quotes are available.
eMaint
Description:
eMaint, part of the Fluke Corporation, is a flexible and powerful CMMS software that supports various maintenance management needs, from work order management to predictive maintenance.
Pros:
Highly customizable, strong customer support, and good integration capabilities.
Cons:
It can be overwhelming for new users.
Mainly Used For:
Manufacturing, facilities management, food & beverage.
Pricing Package:
Subscription-based pricing with various plans.
Dude Solutions
Description:
Dude Solutions offers a suite of CMMS solutions tailored to specific industries, including education, healthcare, government, and manufacturing.
Pros:
Industry-specific solutions, intuitive interface, good support.
Cons:
Pricing can be high for smaller organizations.
Mainly Used For:
Education, healthcare, and government.
Pricing Package:
Subscription-based pricing is customized based on industry needs.
Implementation and Integration Considerations
Data Migration and Asset Inventory
Data Preparation: Before implementation, ensure that all existing maintenance data, asset records, and historical information are accurate and up-to-date. Clean and organize the data to facilitate a smooth migration.
Asset Inventory: Thoroughly inventory every asset that the CMMS will be used to manage. Gather comprehensive details about every asset, such as its location, state, and maintenance history.
Data Mapping: This step maps existing data to the new CMMS structure. It ensures that all data fields align correctly and that no critical information is lost during the migration process.
Integration with Existing Systems (ERP, EAM, IoT, etc.)
System Compatibility: Assess how well the CMMS works with current systems, including IoT (Internet of Things) platforms, EAM (Enterprise Asset Management), and ERP (Enterprise Resource Planning).
Integration Strategy: Develop an integration strategy that outlines how the CMMS will interact with other systems. This strategy should include data sharing, real-time updates, and automated workflows.
APIs and Connectors: To facilitate seamless integration, utilize APIs (Application Programming Interfaces) and pre-built connectors provided by the CMMS vendor. Custom integrations may be necessary for specialized requirements.
User Training and Change Management
Training Programs: Provide thorough training courses for managers, administrators, maintenance personnel, and other users. The training should cover system functioning, best practices, and troubleshooting advice.
Change Management: Implement a change management plan to address the organizational impact of the new CMMS. Share the system’s advantages with all relevant parties and assist in facilitating the changeover.
Ongoing Support: Ensure training and continuous support are offered to handle any problems that may arise after installation. Helpdesk support, user manuals, and refresher classes can all fall under this category.
Security and Access Control
User Roles and Permissions: Define user roles and permissions to ensure that users only have access to the information and features required for their jobs. This preserves data integrity and safeguards sensitive information.
Data Security: Implement strong security measures to shield data from threats, breaches, and unauthorized access. This covers secure login procedures, encryption, and frequent security audits.
Compliance: Verify that the CMMS conforms with all applicable data protection laws and industry standards, including HIPAA, ISO, and GDPR.
Customization and Configuration
Tailored Workflows: Customize the CMMS workflows to align with your organization’s maintenance processes and procedures. This customization ensures that the software supports your unique operational requirements.
Configuration Options: Utilize the configuration options provided by the CMMS to set up asset hierarchies, maintenance schedules, notification settings, and reporting templates according to your needs.
Vendor Support: Work closely with the CMMS vendor to leverage their expertise during the customization and configuration process. Vendor support can address any challenges and ensure the system is optimized for your organization.
CMMS Implementation Best Practices
To ensure a smooth and successful CMMS (Computerized Maintenance Management System) implementation, follow these best practices:
Define Clear Goals and Objectives
Set Specific Goals: Clearly define what you aim to achieve with the CMMS implementation. This could include improving maintenance efficiency, reducing downtime, enhancing asset management, or ensuring compliance.
Measurable Objectives: Establish measurable objectives to track progress and success. Examples include reducing maintenance costs by a certain percentage, increasing equipment uptime, or improving response times for work orders.
Involve Key Stakeholders and End-Users
Stakeholder Engagement: Involve key stakeholders to ensure their buy-in and support from the beginning. This includes maintenance managers, technicians, IT staff, and executive leadership.
End-User Input: Gather input from end-users who will interact with the CMMS daily. Their insights can help tailor the system to meet practical needs better and enhance usability.
Establish a Dedicated Implementation Team
Implementation Team: Form a dedicated implementation team comprising members from various departments, including maintenance, IT, and operations. This team will oversee the project, make decisions, and ensure smooth execution.
Project Manager: Assign a project manager to coordinate activities, manage timelines, and ensure communication among team members.
Develop a Comprehensive Implementation Plan
Detailed Planning: Make a thorough implementation strategy that describes every stage of the project, from the first analysis to the final deployment. Provide deadlines, checkpoints, and roles.
Resource Allocation: Determine and allot the resources, such as staff, funds, and technology, required to support the implementation process.
Conduct Thorough Testing and User Acceptance Testing
System Testing: Conduct thorough testing of the CMMS to ensure it meets your needs and operates as intended. Test every function, including reporting, asset tracking, and work order management.
User Acceptance Testing (UAT): Engage end users in user acceptance testing (UAT) to ensure the system satisfies their needs and is easy to use. Address any concerns or suggestions prior to the complete rollout.
Provide Adequate Training and Support
Training Programs: Develop and deliver training programs tailored to different user roles. Ensure that all users, from technicians to managers, understand how to use the CMMS effectively.
Ongoing Support: Provide ongoing support to address any issues that arise post-implementation. This can include helpdesk services, refresher courses, and access to user manuals and tutorials.
Training and Support for CMMS Users
Ensuring the successful adoption and application of Computerized Maintenance Management System (CMMS) software requires adequate training and support. Here are a few things to think about:
Vendor-provided training (On-site, Online, or Self-Paced)
On-Site Training: Many vendors offer on-site training sessions where their experts visit your location to provide hands-on training tailored to your needs. This approach allows for personalized instruction and immediate feedback.
Online Training: Webinars and virtual workshops are two easy and adaptable ways to receive training. They are perfect for geographically distributed teams and may be arranged to accommodate various time zones.
Self-Paced Training: Vendors frequently offer self-paced training modules to enable customers to learn at their own pace. These modules frequently incorporate interactive lessons, videos, and quizzes to support learning.
In-House Training and Knowledge Transfer
Train-the-Trainer Programs: Implement a train-the-trainer approach, where a few key staff members receive in-depth training from the vendor and then train other employees. This method ensures that knowledge is disseminated effectively across the organization.
Internal Workshops: Organize frequent internal workshops to inform staff members about new features, recommended procedures, and troubleshooting techniques. These meetings can also function as forums for discussing problems and solutions.
User Manuals and Documentation
Comprehensive Documentation: Ensure that detailed user manuals and documentation are available. These resources should cover all aspects of the CMMS, from basic functions to advanced features, and be easily accessible to all users.
Quick Reference Guides: Develop quick reference guides for common tasks and processes. These can be handy for new users and provide immediate assistance for frequently performed actions.
Online Help and Support Resources
Knowledge Base: Establish an online knowledge base where users can access how-to articles, troubleshooting advice, and answers to frequently asked issues. This resource ought to be updated frequently and searchable.
Community Forums: Encourage users to join online community forums so they may converse with other CMMS users, exchange stories, and ask questions. These discussion boards encourage a feeling of camaraderie and group problem-solving.
Customer Support and Maintenance Agreements
Helpdesk Support: Guarantee that consumers may contact a dependable helpdesk representative for assistance with technical problems and inquiries. You can get this help by phone, email, or live chat.
Maintenance Agreements: If the vendor offers frequent software updates, bug patches, and continuous technical assistance, consider signing up for a maintenance agreement. This will keep the CMMS current and operational.
Service Level Agreements (SLAs): Establish clear SLAs with the vendor that outline the expected response times and support levels. This helps manage expectations and ensures timely assistance when needed.
Future Trends in CMMS Technology
The landscape of computerized maintenance management system (CMMS) software is always changing due to technological breakthroughs and shifting demands in the business. The following are some emerging themes that will influence maintenance management going forward:
Integration with the Internet of Things (IoT) and Predictive Maintenance
Sensor Integration: CMMS platforms will increasingly integrate with IoT sensors embedded in equipment to collect real-time asset performance and health data.
Predictive Maintenance: By analyzing IoT data, CMMS systems will be able to anticipate equipment problems before they happen, enabling proactive maintenance interventions and reducing downtime.
Machine Learning and Artificial Intelligence (AI) for Predictive Analytics
AI-Powered Insights: AI and machine learning algorithms will analyze vast maintenance data to identify patterns, trends, and anomalies, enabling more accurate predictive analytics and actionable insights.
Optimized Maintenance Strategies: AI-driven CMMS systems will use predictive analytics to optimize maintenance schedules, resource allocation, and inventory management, improving efficiency and reducing costs.
Mobile and Wearable Technology for Field Service
Mobile Apps: CMMS solutions will offer advanced mobile applications that enable technicians to access work orders, asset information, and documentation on smartphones and tablets, facilitating real-time collaboration and communication.
Wearable Devices: Wearable technology, such as smart glasses and augmented reality (AR) headsets, will enhance field service operations by providing hands-free access to maintenance instructions, schematics, and remote support.
Cloud-Based and SaaS CMMS Solutions
Scalability and Accessibility: The scalability, flexibility, and accessibility of cloud-based CMMS platforms will propel their continued rise in popularity. The solution is accessible to organizations from any location with an internet connection, increasing the effectiveness of remote maintenance management.
Cost-Effectiveness: Software-as-a-Service (SaaS) models will dominate the CMMS market, offering subscription-based pricing that eliminates the need for upfront investment in hardware and software licenses.
Augmented Reality (AR) for Enhanced Maintenance Workflows
AR-Assisted Maintenance: AR technology will revolutionize maintenance workflows by overlaying digital information, such as equipment schematics, instructions, and diagnostic data, onto the physical environment.
Remote Assistance: AR-enabled CMMS systems will enable technicians to receive remote assistance from experts, who can provide guidance and support in real-time. This will reduce the need for on-site visits and improve resolution times.
FAQs
What distinguishes EAM software from CMMS software?
CMMS (Computerized Maintenance Management System) software focuses on managing maintenance operations. In contrast, EAM (Enterprise Asset Management) software encompasses a broader range of asset lifecycle management functions, including maintenance, inventory, and procurement.
Can CMMS software be integrated with existing systems?
Yes, most modern CMMS solutions offer integration capabilities with other systems, such as ERP, EAM, IoT platforms, and building management systems (BMS), to facilitate data exchange and streamline workflows.
How does CMMS software support preventive maintenance?
CMMS software enables organizations to schedule and automate preventive maintenance tasks based on time-based or condition-based triggers, helping to extend asset lifespan and reduce unplanned downtime.
What are the typical deployment options for CMMS software?
CMMS software can be deployed on-premises, hosted in the cloud, or offered as a Software-as-a-Service (SaaS) solution, providing flexibility based on an organization’s specific needs and preferences.
How can CMMS software improve compliance and regulatory adherence?
CMMS software helps organizations maintain detailed maintenance records, track asset histories, and generate reports, enabling them to demonstrate compliance with industry regulations, safety standards, and best practices.
Conclusion
CMMS software implementation may transform maintenance processes, boost equipment uptime, and improve operational efficiency in various sectors. Organizations may select the best CMMS system to make data-driven choices, optimize asset management, and streamline maintenance procedures by knowing the essential features, advantages, and selection criteria. Combining CMMS with IoT, AI, and other cutting-edge technologies will improve maintenance capabilities and provide even more insights as technology develops. Purchasing a strong CMMS system is a wise strategic move that can help with long-term profitability, cost reductions, and gaining a competitive edge in the dynamic business environment.