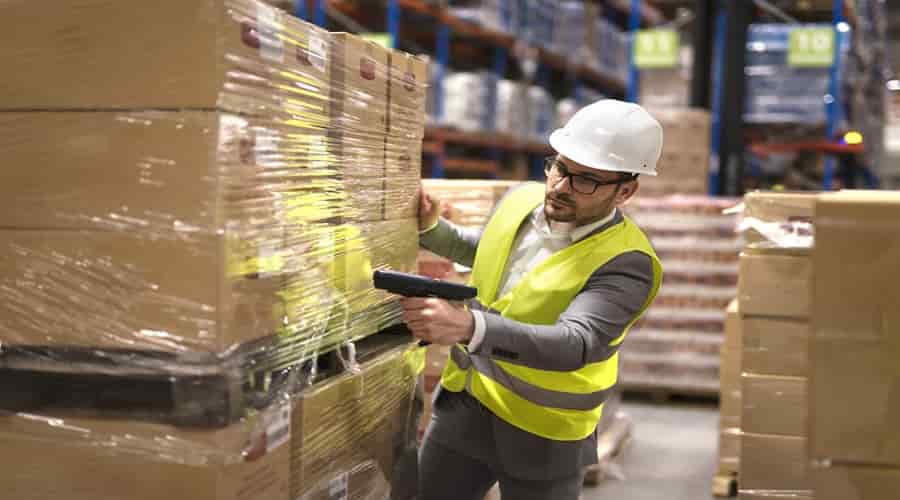
Warehouse Management System: Boost Efficiency with Real-Time
A Warehouse Management System (WMS) serves as the backbone of modern warehousing operations, revolutionizing how businesses manage their inventory, streamline processes, and meet customer demands. Imagine a sophisticated toolkit designed to orchestrate every aspect of warehouse logistics seamlessly. From receiving goods to dispatching orders, a WMS empowers businesses to optimize space, enhance inventory accuracy, and boost productivity. By providing real-time visibility into inventory levels, automating tasks, and enabling efficient resource allocation, WMS transforms warehouses into efficient operation hubs, ensuring timely deliveries and satisfied customers.
What is Warehouse Management?
The process of supervising and managing the flow, storage, and distribution of items inside a warehouse or distribution center is known as warehouse management. It includes a range of tasks like order processing, picking, packing, shipping, putaway, receiving, and inventory management. Optimizing warehouse space utilization, reducing handling expenses, and guaranteeing precise and fast customer order fulfillment are the main objectives of effective warehouse management.
Benefits of Implementing a Warehouse Management System
Increased inventory accuracy and visibility:
WMS enables real-time tracking of inventory movements and levels, lowering errors and guaranteeing precise stock counts.
Visibility into inventory allows for better planning, forecasting, and preventing stockouts or overstock situations.
Optimized warehouse operations and improved productivity:
WMS streamlines warehouse processes such as receiving, picking, packing, and shipping, leading to increased efficiency.
Automating tasks like inventory replenishment and order routing reduces manual effort and speeds up operations.
Enhanced order fulfillment speed and accuracy:
With WMS, orders are processed faster and more accurately, leading to quicker fulfillment and fewer errors.
Advanced features like wave picking and batch processing optimize order picking routes and sequencing, further improving efficiency.
Reduced labor costs and operational expenses:
Automation and optimization of warehouse tasks reduce labor requirements and associated costs.
Efficient use of resources and reduced error rates minimize rework and operational expenses, leading to cost savings.
Better space utilization and inventory management:
WMS provides insights into warehouse layout and storage capacity, enabling optimal space utilization and inventory placement.
Features like slotting optimization help organize inventory for easy access and maximize storage efficiency.
Improved customer satisfaction and service levels:
Faster order processing, accurate inventory information, and on-time deliveries increase customer satisfaction.
WMS enables improved order accuracy, reduced lead times, and better customer communication, enhancing overall service levels.
Real-time data and reporting for informed decision-making:
WMS generates real-time data on key warehouse metrics like inventory levels, order status, and performance indicators.
Customizable reporting tools provide insights into warehouse operations, helping in decision-making and continuous improvement.
Compliance with industry regulations and standards:
WMS ensures compliance with regulatory requirements and industry standards related to inventory management, traceability, and safety.
Features such as lot tracking and serial number management facilitate compliance with product handling and tracking regulations.
Key Features of a Warehouse Management System
Inventory management and tracking:
Enables precise monitoring and tracking of inventory locations, movements, and levels inside the warehouse.
Provides visibility into stock quantities, ensuring optimal inventory control and preventing stockouts or overstock situations.
Receiving and putaway processes:
Facilitates efficient handling of incoming goods by managing receiving workflows and documenting receipt details.
It supports the organized storage of received items in designated storage locations based on predefined criteria like SKU, size, or demand.
Order processing and fulfillment:
Manages the entire order fulfillment process from receipt to shipment, ensuring timely and accurate order processing.
Automates order prioritization, allocation, and status updates to streamline fulfillment operations.
Pick, pack, and ship operations:
Optimizes picking processes by generating efficient pick routes, batch picking, or wave picking strategies.
Supports packing and shipping activities with tools for packaging optimization, labeling, and carrier selection.
Labor management and task assignment:
Enables efficient allocation of tasks and resources by tracking labor productivity and assigning tasks based on workload and skill levels.
Provides visibility into labor performance metrics, allowing for performance monitoring and optimization.
Warehouse layout and slotting optimization:
Helps design an efficient warehouse layout by defining storage zones and aisles and picking locations.
Optimizes inventory slotting based on SKU velocity, storage requirements, and order-picking patterns.
Real-time inventory visibility and reporting:
Provides real-time visibility into the locations, movements, and inventory levels throughout the warehouse.
Generates customizable reports and dashboards to monitor key performance metrics, track inventory accuracy, and identify areas for improvement.
Integration with other systems (e.g., ERP, TMS, WCS):
Allows for easy data interchange and process synchronization with other enterprise systems, including Warehouse Control Systems (WCS), Transportation Management Systems (TMS), and Enterprise Resource Planning (ERP).
Ensures data consistency and accuracy by facilitating communication between systems within the supply chain ecosystem.
Mobile device support for real-time data access:
Provides mobile applications or interfaces for warehouse personnel to access real-time data, perform tasks, and receive updates on the go.
Enables barcode scanning, RFID technology, or voice-directed picking for improved accuracy and efficiency in warehouse operations.
Types of Warehouse Management System
On-premises WMS:
These systems are installed and maintained on the company’s servers and infrastructure, providing complete control over customization and data security.
On-premises WMS solutions are typically preferred by organizations with specific security or compliance requirements that necessitate hosting data internally.
Cloud-based WMS:
Cloud-based WMS is available as a Software-as-a-Service (SaaS) solution that can be accessed online and is hosted by the provider.
This type of WMS reduces upfront costs and IT overhead since there’s no need to invest in hardware or server maintenance.
Cloud-based WMS solutions offer scalability, allowing businesses to adjust resources based on changing needs easily.
Standalone WMS:
Designed for specific warehouse operations, standalone WMS systems focus on core functionalities such as inventory management and order fulfillment.
These systems are suitable for smaller businesses or warehouses with straightforward needs that may not require the advanced features of integrated solutions.
Integrated WMS:
Vendors offer a wider range of supply chain management solutions, of which integrated WMS solutions are a part.
They offer seamless integration with other modules, such as transportation management, labor management, and Enterprise Resource Planning (ERP) systems.
Integrated WMS solutions provide end-to-end visibility and control over the entire supply chain, streamlining operations and improving efficiency.
Implementation Process
Assessment and planning:
Evaluate current warehouse operations to identify pain points, inefficiencies, and areas for improvement.
Define requirements and objectives for the new WMS, considering scalability, integration capabilities, and budget constraints.
Develop an implementation roadmap outlining key milestones, timelines, and responsibilities to ensure a smooth transition.
System selection:
Research and evaluate different WMS solutions available in the market, considering factors like features, scalability, vendor reputation, and compatibility with existing systems.
Involve departmental stakeholders to get feedback and ensure the chosen WMS satisfies user demands.
Narrow down options and conduct demonstrations or trials to assess the usability and functionality of each solution before making a final decision.
Configuration and customization:
Work closely with the WMS vendor or implementation partner to configure the system according to your business processes and workflows.
Customize the WMS interface, data fields, and reports to align with your organization’s terminology and requirements.
Test the configured system to ensure it meets the agreed-upon specifications and addresses the identified business needs.
Data migration:
Transfer existing data from legacy systems or spreadsheets into the new WMS, including inventory records, customer information, and historical transactions.
Before importing data into the new system, clean and validate it to ensure its accuracy and completeness.
Develop a data migration plan with clear timelines and checkpoints to minimize disruption to operations during the transition.
User training:
Provide comprehensive training sessions for warehouse staff to familiarize them with the functionalities and features of the new WMS.
Training programs should be customized for various user roles and skill levels, encompassing subjects like inventory control, order processing, system navigation, and reporting.
Provide continuing assistance and resources (e.g., training manuals or online tutorials) to reinforce learning and resolve any queries or issues.
Testing and validation:
Conduct thorough testing of the configured WMS to validate its functionality, performance, and compatibility with existing systems.
Create test scenarios and scripts to simulate real-world warehouse operations and verify that the system behaves as expected in various scenarios.
Engage end-users in user acceptance testing (UAT) to gather feedback and ensure the WMS meets their needs and expectations before finalizing deployment.
Go-live and support:
Launch the WMS using a phased or big-bang approach, depending on the complexity of the implementation and the organization’s readiness.
Provide ongoing support and maintenance through the WMS vendor’s support services or an in-house IT team to address any issues or technical challenges that arise post-implementation.
Monitor system performance and user feedback closely during the initial period after going live, making adjustments to optimize the WMS and maximize its effectiveness in supporting warehouse operations.
Integration with Other Systems
To maximize efficiency and data visibility, a WMS should seamlessly integrate with other systems within the supply chain ecosystem, such as:
Enterprise Resource Planning (ERP) systems:
Integration with ERP systems allows for seamless exchange of data related to inventory, sales orders, purchase orders, and financial transactions.
This integration ensures information synchronization between the WMS and ERP, enabling accurate forecasting, planning, and resource allocation across the organization.
Transportation Management Systems (TMS):
Integration with TMS enables coordination between warehouse operations and transportation activities, such as shipment scheduling, carrier selection, and route optimization.
WMS-TMS integration improves overall logistics efficiency and customer service by sharing data on order status, inventory availability, and delivery schedules.
Warehouse Control Systems (WCS):
Integration with WCS facilitates real-time communication between the WMS and automated warehouse equipment, such as conveyors, sorters, and AS/RS systems.
This integration ensures seamless coordination of material flow and task execution within the warehouse, optimizing throughput and minimizing bottlenecks.
Labor Management Systems (LMS):
Integration with LMS enables the WMS to capture labor data such as productivity, attendance, and performance metrics.
WMS-LMS integration helps with workforce planning, scheduling, and performance monitoring by correlating labor information with warehouse activities and workflows.
Yard Management Systems (YMS):
Integration with YMS allows for efficient trailer movement and parking management within the warehouse yard.
By sharing data on inbound and outbound shipments, appointment scheduling, and dock availability, WMS-YMS integration optimizes yard operations and reduces congestion.
Electronic Data Interchange (EDI) platforms:
Electronic interchange of business documents with trading partners, including purchase orders, invoices, and shipment notices, is made possible by integration with EDI platforms.
WMS-EDI integration automates order processing and fulfillment, reduces manual data entry errors, and improves supply chain visibility and responsiveness.
E-commerce platforms and order management systems:
E-commerce platform and order management system integration make processing and fulfilling orders easier for both online and offline sales channels.
By synchronizing inventory levels, order status, and customer information, WMS-E-commerce integration enables efficient omnichannel fulfillment and enhances customer satisfaction.
Warehouse Management System Example
Oracle Warehouse Management (Warehouse Management System):
Oracle WMS is a feature-rich cloud-based system that increases inventory control and expedites warehouse operations.
It offers advanced features such as inventory tracking, order fulfillment, labor management, and real-time analytics.
SAP Extended Warehouse Management (EWM):
SAP EWM is an integrated solution that provides end-to-end visibility and control over warehouse processes.
It offers inbound and outbound processes, storage and inventory management, labor optimization, and yard logistics functionalities.
HighJump Warehouse Management System (Warehouse Management System):
HighJump WMS is a flexible and scalable solution that helps businesses optimize warehouse operations and improve efficiency.
It provides functions including labor management, order processing, inventory tracking, and connection with other supply chain systems.
Warehouse Management System Selection Criteria
Functionality and Features:
Assess whether the WMS offers the core functionalities required for your warehouse operations, such as inventory management, order processing, picking, packing, and shipping.
Look for advanced features like barcode scanning, batch processing, wave picking, slotting optimization, and real-time inventory visibility.
Scalability and Flexibility:
Consider the scalability of the WMS to accommodate your business growth and evolving needs.
Evaluate whether the system can adapt to warehouse size, volume, product mix, and changes in operational requirements.
Integration Capabilities:
Ensure the WMS seamlessly integrates with other systems within your supply chain ecosystem, such as ERP, TMS, WCS, LMS, and e-commerce platforms.
Check for pre-built integrations, APIs, and compatibility with industry-standard protocols like EDI.
Ease of Use and User Experience:
Look for a WMS with an intuitive user interface, navigation, customizable dashboards, and reporting capabilities.
Consider the accessibility of user guides, training materials, and customer assistance to guarantee a seamless deployment and adoption process.
Technology and Infrastructure:
Assess whether the WMS is deployed on-premises or in the cloud, and evaluate the associated benefits and challenges of each deployment option.
Consider the technology stack, system architecture, security measures, and performance capabilities of the WMS.
Cost and ROI:
Evaluate the total cost of ownership (TCO) of the WMS, including implementation, licensing, maintenance, and support fees.
Determine the prospective ROI by projecting savings, increasing productivity, and optimizing operational effectiveness.
Vendor Reputation and Support:
Research the WMS vendor’s reputation and track record, including customer reviews, case studies, and industry recognition.
Evaluate the vendor’s expertise, responsiveness, and availability of support services, including implementation assistance, training, and ongoing technical support.
Compliance and Industry-Specific Requirements:
Ensure that the WMS complies with regulatory requirements and industry standards relevant to your business, such as FDA regulations for food and pharmaceuticals or GMP guidelines for manufacturing.
Consider any specific features or functionality required for your industry or niche, such as lot tracking, serial number management, or cold chain logistics support.
Performance Metrics and KPIs
Inventory accuracy:
Percentage of inventory items accurately recorded in the system compared to physical inventory counts.
KPI: Inventory Accuracy Rate (%) = (Number of accurate inventory items / Total number of inventory items) x 100
Order fulfillment rate and cycle time:
Percentage of customer orders successfully fulfilled within the specified timeframe.
Average time taken to process and fulfill an order from receipt to shipment.
KPI: Order Fulfillment Rate (%) = (Number of fulfilled orders / Total number of orders) x 100
KPI: Order Cycle Time (Days) = Average time from order receipt to order shipment
Picking and away productivity:
Number of order lines or units picked or put away per hour or labor hour.
KPI: Picking Productivity (Lines/Hour) = Number of order lines picked / Total picking time (hours)
KPI: Putaway Productivity (Units/Hour) = Number of units put away / Total putaway time (hours)
Space utilization and cube utilization:
Percentage of available warehouse space or storage cube effectively utilized for storing inventory.
KPI: Space Utilization Rate (%) = (Used storage space / Total available storage space) x 100
KPI: Cube Utilization Rate (%) = (Used storage cube volume / Total available storage cube volume) x 100
Labor costs and efficiency:
Total labor costs incurred in warehouse operations, including wages, benefits, and overhead expenses.
Labor productivity is measured as output (e.g., order lines picked) per labor hour or labor cost.
KPI: Labor Cost per Unit = Total labor costs / Total units processed
KPI: Labor Productivity (Units/Labor Hour) = Number of units processed / Total labor hours
Transportation costs and carrier performance:
Total transportation costs incurred for inbound and outbound shipments, including freight charges and carrier fees.
The percentage of timely shipments measures on-time delivery performance and carrier reliability.
KPI: Transportation Cost as a Percentage of Sales = (Total transportation costs / Total sales) x 100
KPI: On-time Delivery Rate (%) = (Number of on-time deliveries / Total number of deliveries) x 100
Customer satisfaction and service levels:
Customer satisfaction surveys or feedback scores measure overall satisfaction with order accuracy, timeliness, and service quality.
Percentage of orders delivered complete and on time, as per customer expectations.
KPI: Customer Satisfaction Score (CSAT) = Average rating or score from customer feedback surveys
KPI: Order Perfect Fulfillment Rate (%) = (Number of orders delivered complete and on time / Total number of orders) x 100
Warehouse Layout and Design
Inventory Storage Strategy:
Choose the best type of storage for your goods, whether mezzanine, pallet flow racks, bulk, or selective racking.
Organize inventory based on factors like SKU velocity, size, and handling requirements to minimize travel time and maximize picking efficiency.
Traffic Flow and Material Handling:
Design clear aisles and pathways to ensure smooth traffic flow for pedestrians and equipment such as forklifts and pallet jacks.
Optimizing the layout for efficient material handling processes, including receiving, putaway, picking, packing, and shipping, will minimize congestion points and bottlenecks.
Zone Segmentation:
Divide the warehouse into functional zones based on the operations performed, such as receiving, storage, picking, packing, and shipping.
Allocate specific areas for high-traffic zones like receiving docks, shipping docks, and staging areas to streamline workflow and minimize cross-traffic.
Slotting Optimization:
Implement slotting strategies to organize inventory within storage locations based on SKU velocity, turnover rate, and picking frequency.
To cut down on trip time and improve picking efficiency, arrange quickly moving commodities closer to the shipping area and picking zones.
Vertical Space Utilization:
Use vertical space efficiently by utilizing tall storage racks, mezzanine levels, or automated storage and retrieval systems (AS/RS) to maximize storage capacity.
Consider factors like ceiling height, load-bearing capacity, and equipment accessibility when designing vertical storage solutions.
Safety and Compliance:
Adhere to industry norms and safety laws by implementing safety measures such as emergency evacuation routes, safety barriers, and aisle markers.
Provide adequate lighting, ventilation, and fire protection systems to maintain a safe working environment for warehouse personnel and protect inventory from damage or loss.
Technology Integration:
Integrate technology solutions such as Warehouse Management Systems (WMS), barcode scanning, RFID tracking, and automation equipment to enhance visibility, accuracy, and efficiency in warehouse operations.
Design the layout considering the placement of technology infrastructure and power sources to support seamless integration and operation.
Future Expansion and Adaptability:
Plan for future growth and expansion by designing a flexible layout that can accommodate changes in inventory volume, product mix, and operational requirements.
Provide scalable, modular design components that are simple to expand or reconfigure to meet changing business requirements.
Challenges in Warehouse Management System Implementation
Change management and user adoption:
Resistance to change among employees who are accustomed to existing processes and systems.
More support and buy-in from important stakeholders and users are needed.
Inadequate training and communication strategies to prepare users for the transition to the new WMS.
Data quality and integrity issues:
Inaccurate or incomplete data in existing systems leads to discrepancies and inventory record errors.
Data cleansing and migration challenges include data formatting, normalization, and deduplication.
Lack of data governance policies and procedures to ensure data consistency and reliability.
Integration complexities with existing systems:
Compatibility issues between the WMS and other enterprise systems, such as ERP, TMS, and WCS.
Customization requirements to integrate the WMS with legacy systems or third-party applications.
Dependency on external vendors or IT resources for implementing and maintaining integrations.
Resource constraints and budget limitations:
Limited availability of skilled personnel with expertise in WMS implementation and project management.
Budget constraints affect the scope and timeline of the implementation project.
Trade-offs between investing in additional features or functionalities versus staying within budget constraints.
Warehouse layout and infrastructure limitations:
Physical constraints such as limited space, layout inefficiencies, or outdated infrastructure.
Inadequate equipment or technology infrastructure to support WMS functionality, such as barcode scanners, RFID readers, or wireless networks.
Requirements for retrofitting or redesigning the warehouse layout to align with WMS workflows and processes.
Compliance with industry regulations and standards:
Adherence to regulatory requirements and industry standards governing inventory management, data security, and workplace safety.
The complexity of compliance requirements across different geographic regions or industry sectors.
Challenges in configuring the WMS to support specific compliance requirements and reporting obligations.
Future Trends in Warehouse Management System
Increased adoption of cloud-based and SaaS WMS solutions:
Organizations are increasingly moving towards cloud-based and Software-as-a-Service (SaaS) WMS solutions for their scalability, flexibility, and cost-effectiveness.
Cloud-based WMS is a desirable alternative for companies of all sizes because it provides simpler setup, automatic upgrades, and access from any location with an internet connection.
Integration with advanced technologies like IoT, robotics, and automation:
WMS will continue combining cutting-edge technology like robotics, automation systems, and Internet of Things (IoT) sensors to improve efficiency and optimize warehouse operations.
IoT-enabled devices facilitate proactive decision-making and optimization by offering real-time data on inventory levels, equipment status, and environmental conditions.
Utilizing machine learning and predictive analytics to forecast and optimize demand:
WMS will leverage predictive analytics and machine learning algorithms to analyze historical data, detect patterns, and more accurately forecast future demand.
Machine learning algorithms will help optimize order fulfillment, warehouse layout, and inventory replenishment in response to seasonality, market trends, and consumer behavior.
Augmented reality (AR) and voice-based technologies for hands-free operations:
AR technology will revolutionize warehouse operations by overlaying digital information, instructions, and visual aids onto the physical environment.
Voice-based technologies, combined with natural language processing (NLP) and speech recognition, will enable hands-free and eyes-free interactions, improving worker productivity and safety.
Improved traceability and visibility throughout the whole supply chain:
WMS will track and monitor inventory movements in real-time, giving customers and suppliers end-to-end visibility and traceability throughout the supply chain.
Integration with supply chain partners and stakeholders will enable seamless information exchange and collaboration, reducing lead times and enhancing responsiveness to customer demands.
Sustainability and eco-friendly warehouse practices:
WMS will support sustainability initiatives by optimizing resource utilization, reducing waste, and minimizing environmental impact.
Eco-friendly warehouse practices such as energy-efficient lighting, recycling programs, and sustainable packaging will be integrated into WMS workflows to promote environmental stewardship and corporate social responsibility.
FAQs
What is the typical implementation timeline for a WMS?
The implementation schedule may change depending on the extent of the project, the degree of customisation needed, and the complexity of your operations. On average, a good WMS implementation can take several months to a year.
Can a WMS be used for multiple warehouse locations?
Most modern WMS solutions support multi-site and multi-warehouse operations, providing centralized management and visibility across various locations.
How often should a WMS be upgraded or replaced?
The frequency of upgrades or replacements depends on your business needs, technological advancements, and the vendor’s support lifecycle. Evaluating and upgrading your WMS every 5-7 years is generally recommended to take advantage of new features and capabilities.
Can a WMS be integrated with existing systems like ERP and TMS?
Modern WMS solutions are designed to integrate with various other systems within the supply chain ecosystem, such as ERP, TMS, WCS, and e-commerce platforms. This integration ensures seamless data flow and visibility across different processes.
Conclusion
An effective warehouse management system is essential for success in the hectic field of supply chain management and logistics. A well-executed WMS can offer a major competitive advantage by maximizing resource use, increasing inventory accuracy, and streamlining processes. Investing in a strong WMS will be essential to attaining operational efficiency, cutting costs, and providing exceptional customer service as organizations adjust to changing customer needs and technology improvements.